做好APS生产计划和控制的核心步骤
生产计划和控制的的核心步骤
- 主数据准备
- 静态数据
- 动态数据准备
- 主计划(完工计划)编制准备好主数据后,可以编制生产计划了。
1)确认客户需求确认需求是编制生产计划的第一步。
一般而言,工厂是MTO(订单式)、MTS(备库式)的混合模式。
订单式(MTO)模式时,客户订单就是客户需求,具有非常明确的需求的品种、需求的时间、需求的数量(隐含了技术和质量指标)。
备库式(MTS)模式时,俗称的是补库模式,其客户需求的表现模式,是内部的补库订单,或称之为预测订单。
很多企业还会把这个需求做的更加复杂些,分为“销售订单”、“备货订单”、“补库订单”、“备料订单”等方式,本质还是“订单”、“备库”两种。
备库式(MTS)采用预测方式确认需求时,最好采用滚动预测方式:即按照一个“固定的预测周期(如三个月)”、“固定的预测间隔(如间隔两周)”实现滚动预测,并锁死预测、和预测校正的方法,以确保预测的相对科学性。 需求管理是十分重大事项,是确定PSI(P生产、S出运、I库存)的第一步,是非常核心的关键环节。
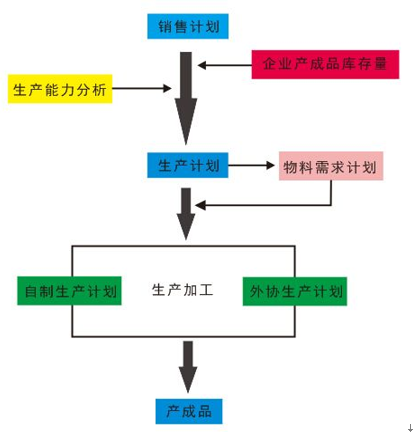
2)产销平衡
确定需求时,需要对物料供应、内部产能进行平衡。如果工厂上线了APS高级计划和排程,则这一过程相对容易:
- 确认需求并录入APS
- APS运算并发出异常报表(延误警告报表)
- 调整需求并录入APS
- APS重新运算并发出异常宝博鳌
循环1-2次但是,如果没有APS高级计划和排程系统,需要手工进行需求、供应和产能的平衡,其标准步骤如下:
- 识别关键物料的供应量。
- 根据关键物料的供应编制投料品种、时间和数量,实现物料平衡。
- 再根据关键产能设备的约束,前后调整生产任务的投放,以满足产出的要求。
- 如果工厂是多车间的场景,则在车间之间的半成品仓作为缓冲,以平衡车间之间的关键产能设备制约间的冲突,用提前生产储备库存的方式,释放关键设备产能。产、供、销售的平衡,是一项复杂的引擎计算过程,Excel的算力十分有限,所以只能以简化的方式进行:比如,产能采用平均产能、物料就核算关键物料等等,以降低计算难度。
3)编制完工计划
在产、供、销售平衡后,可以编制完工计划。完工计划是一个预期计划,关键的假设如下:
- 不考虑客户需求变动、不考虑产能波动(预设的以外)、不考虑供应商波动,是正常情形下的正常产出。
- 或详细预排程或粗的预排程编制完工计划的周期限制,需要根据业务状态来确定.
白酒的生产周期很长,大约需要5年的时间(60个月),所以主计划的周期至少为一年,并逐步分解。尤其是制曲、制酒和初勾兑,是完全的“推”过程,主计划的时间可以稍长,而成品酒的勾兑、包装过程,大约是10天,可以月来设计,甚至就是10天的循环计划即可,实现动态补库。
汽车零部件行业则刚刚相反,主机厂一般仅仅提供单周锁定+双周滚动的需求计划,则汽车零部件企业不能编制较长期的主计划,而是编制两周的滚动主计划即可,即时响应汽车零部件企业在主机厂边上的库存需求即可。 大量的OEM企业,由于承诺交期较长,一般是30-45天,甚至60天以上的周期,则可以编制以月(4周)的主计划(出运计划),以此形成月出运计划、周大滚动、三天小滚动一天所动的计划,逐步实现不确定-半确定-稳定-锁定的作业计划。
日完工计划,还需要转换为开工计划。制造周期较长的,作业计划的锁定期要稍微变长,采用T+2、T+3模式。
编制的完工计划,可以用“月计划”、“周计划”、“日计划”方式呈现。